Technology provides opportunities
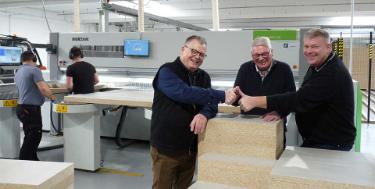
AUBO has invested in a new fully automated storage and cutting system consisting of a Biesse Selco panel saw and a Winstore X2 storage robot. A facility that has made production significantly more efficient. Now it takes 24 hours to cut up what used to be two men's work in 72 hours.
- We are very impressed with our new facility, says director Torben Andersen, but he also states that it is the advice and cooperation with the supplier, combined with the commitment of the employees, that has made the big difference.
AUBO has offered "KITCHENS FOR CONNOISSEURS" for more than three decades. A company that is characterized by West Jutland decency, and where they try to give the customer the best imaginable product. Based on a strategic decision to produce the kitchens themselves, more and more tasks have been insourced in recent years - including cutting sheets. A strategy that gives the company greater flexibility, increased delivery reliability and the opportunity to create its own design. Over time, insourcing has also proven to be solid business. Over the past several years, AUBO has delivered great results and is today known far beyond the country's borders, with Norway as its largest market.
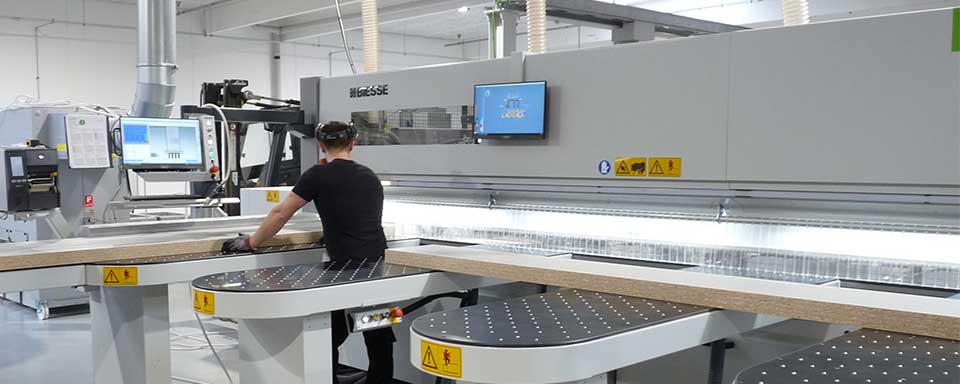
A trip to Italy made the dream come true
AUBO CEO Torben Andersen and production manager had many dreams and plans about how production could be made more efficient. As AUBO has become more and more self-producing, the need for panel cutting and panel storage management has become evident. AUBO's management has been working with Key Account Manager Poul Erik Haurum for many years, and it was therefore obvious to ask for his advice when a new solution had to be found.
- We have always valued mutual trust and respect with our employees and business partners. It is important for us to collaborate with someone who understands our production and can find machines and solutions that fit into the whole picture. - And we know that Poul Erik Haurum from Junget can do that, explains Torben Andersen. - We had no objections, when Junget invited us on a trip to the Italian machine manufacturer Biesse. Here we had the opportunity to see machines that could solve the tasks that we had outlined, says Michael Pedersen, and continues.
- That trip to Italy was a huge eye-opener for us. We went from having thousand ideas to seeing a concrete plant that could solve the task for us.
Here, the AUBO team saw with their own eyes how a new panel handling system and a panel saw could make the entire cutting process more efficient. The machinery they saw at Biesse could, in 24 hours with a 70% occupancy, produce the same as AUBO produced with 2 men in 72 hours. It was an efficiency improvement that the AUBO team could relate to and a good starting point for calculating an attractive business case.
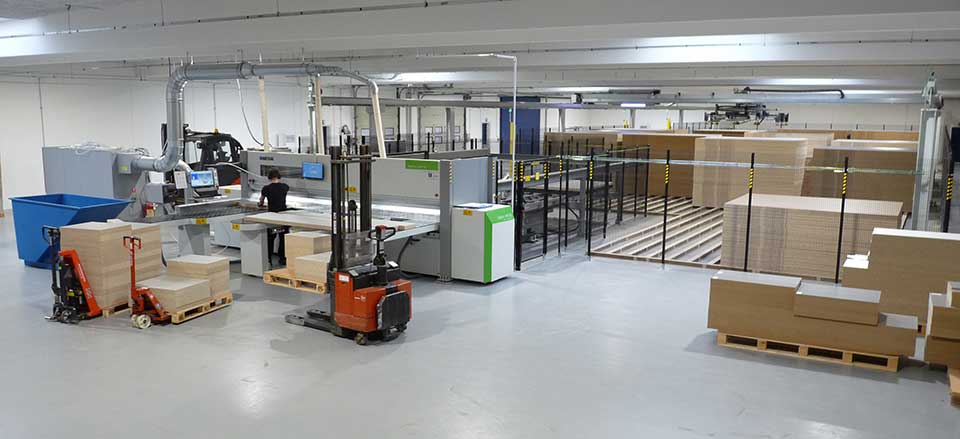
The new Biesse machines move in at AUBO
The fully automatic panel storage consists of a Biesse Winstore X2 storage machine, which can keep track of up to 7,000 panels that must be sorted, stored, and delivered. The storage machine is placed in extension of the Selco WN 6 panel saw, so that it delivers panels to the saw as they are used. This minimizes time waste, and the saw can work non-stop.
The Biesse panel saw has built-in many features, such as a Twin Pusher function, which among other things makes it possible to make both longitudinal and transverse cuts simultaneously. The twin pusher function ensures that the workpieces are placed independently of each other at the correct distance to the saw unit. In this way, the saw can saw workpieces of different sizes in one and the same processing. This significantly increases the productivity of the saw. When the workpieces are finished cutting, the display indicates a colour code. This way, the operator knows how far he has come and where the workpiece belongs. The saw is also equipped with a label printer. Small labels with data and specifications are placed on the items so that they are ready for the next step in production.
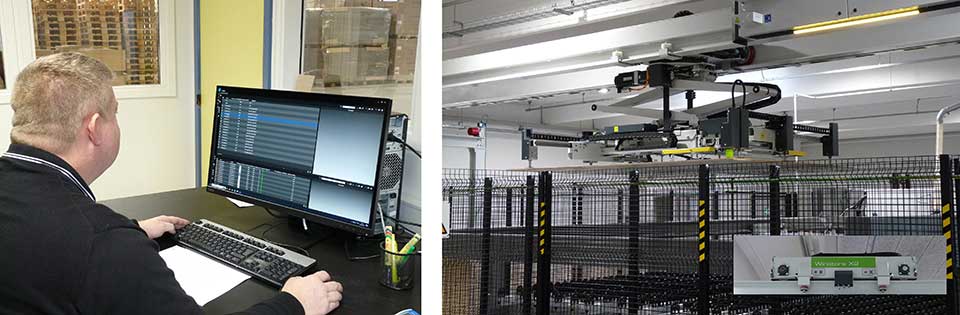
We were good, and now we are even better
In modern production, data integration is what creates a connection from the order system to production and the final delivery of goods. Here, Junget's software engineers have formatted data and created the necessary integration for the new plant.
- The big difference is that before there were few exceptions that each employee just knew by heart. Now all exceptions also must be integrated in the data flow so that the machines can handle the tasks. I thought that we used to be good at production management and data, says Michael Pedersen, but I must state that now we could improve even more.
Software saves 3% material consumption.
- The software on the system is so user-friendly and intelligent that the system can easily be operated even by less educated employees. The degree of "intelligence" in relation to cutting guidance and utilization of the material has resulted in a material saving of approximately 3%. A saving that has come as a positive surprise, explains a satisfied AUBO director, and concludes
- We have made the right investment. We are extremely satisfied with the storage and cutting plant, and the whole process around purchase and installation has been fantastic. And after all, it is the personal advice and the human efforts that have ensured that today we have a production unit that is better than expected.